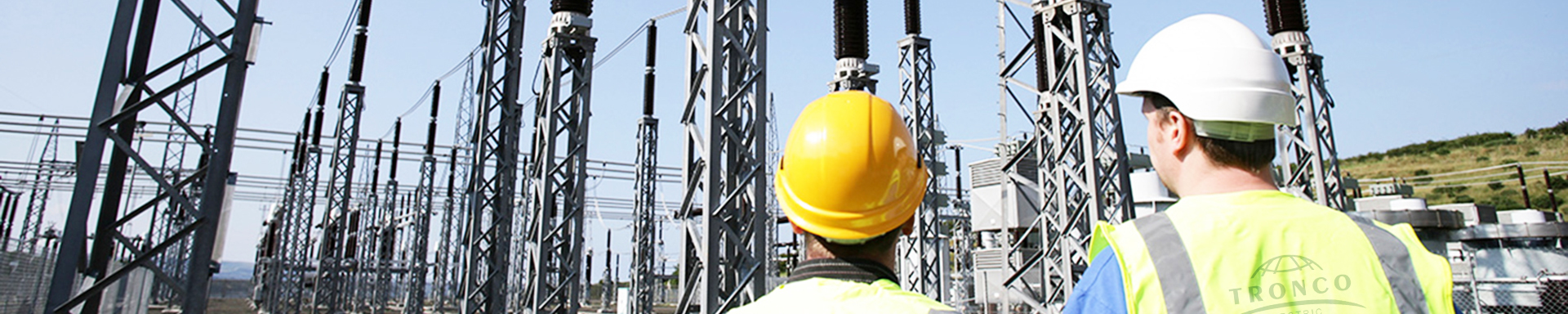
Fabricage van hoogwaardige isolatoren van gehard glas
2022-11-07 20:28Kwaliteit is een maatstaf voor uitmuntendheid en wordt in de elektriciteitsindustrie gebenchmarked met behulp van een verscheidenheid aan nationale of internationale normen zoals ANSI, IEEE, IEC, ASTM, enz. Hoewel het voldoen aan deze normen natuurlijk van cruciaal belang is, zijn de meesten gaan erkennen dat normen tegenwoordig vertegenwoordigen ze slechts minimale prestatie-eisen in een applicatie. Om deze reden proberen zowel fabrikanten als gebruikers de productkwaliteit verder te differentiëren met behulp van verbeterde specificaties. Kwaliteit gaat ook over productie. In dit opzicht richten normen en continue procesverbetering zich op controles en herhaalbaarheid met als doel nul defecten. Uiteindelijk moet kwaliteit het productvermogen en de lange levensduur vertegenwoordigen, naast de naleving van basisnormen en klantspecificaties.
De fabricage van isolatoren van gehard glas bestaat uit twee belangrijke stappen: het vervaardigen van de glazen schaal en vervolgens de montage van metalen hulpstukken op die schaal. De productie vereist gespecialiseerde apparatuur en slechts enkele fabrikanten wereldwijd hebben de middelen en ervaring om beide stappen in één enkele productiefaciliteit uit te voeren. In dit opzicht is het nuttig om de kwaliteit te bestuderen, niet alleen met betrekking tot de fabricage van de geharde glazen schaal, maar ook later tijdens de uiteindelijke montage van de isolator.
De geharde glazen schaal vormt de eigenlijke isolator. Hoewel ook de montage van de fitting en de verlijming ervan belangrijk zijn, moet deze schaal gedurende de gehele levensduur intact blijven om de functionaliteit van het product te waarborgen. Bovendien, als het eenmaal in elkaar is gezet, zal het zelden voorkomen dat de schaal breekt, niet veroorzaakt door een externe gebeurtenis. De algemene verwachting van de industrie is bijvoorbeeld dat minder dan 1 op de 10.000 geïnstalleerde eenheden per jaar spontaan zou versplinteren. Als zodanig is het optreden van zelfvernietiging een aspect van de productie dat de fabriek moet proberen te minimaliseren.
Afgezien van de kritieke schaal, omvatten de hardwarecomponenten van een isolator van gehard glas:
1. Kappen
De dop aan de bovenkant is een nodulair gietijzeren moffitting die is gegalvaniseerd en gemonteerd met een roestvrijstalen borgpen.
2. Spelden
De onderste penfitting is een gesmede stalen kogelverbinding die is verzinkt en gecoat met bitumineuze teer. Er kan ook een opofferingskraag van zink worden toegevoegd voor betere prestaties, vooral in veeleisende serviceomgevingen.
Gaffel-/tongfittingen worden soms gebruikt bij lagere spanningen.
3. Ruw glas en oven
De fabricage van de glazen schaal begint met belangrijke grondstoffen en ingrediënten, waaronder silica, aluminiumoxide, natriumcarbonaat, natriumsulfaat, kalksteen, potas en dolomiet. Cullet (ook wel zaadglas genoemd) is glas dat is gerecycled uit eerdere productie en aan deze grondstoffen is toegevoegd om consistentie van batch tot batch te garanderen. Het mengen van deze materialen is specifiek voor elke fabrikant en ziet kleine variaties in elementen die uit lokale bronnen worden gewonnen of in de oven worden gebruikt. Deze natuurlijke variaties in mineralen verklaren het kleine verschil dat wordt waargenomen in de tint van de glazen isolerende schaal.
Ovens zijn doorgaans grootschalig met een capaciteit van meer dan 100 ton. Voor consistentie is het belangrijk om de temperatuur te handhaven en ook om regelmatig de chemie van de output te controleren, evenals de mix van grondstoffen die wordt ingevoerd. De oven is de eerste mogelijke bron van insluitsels – onvolkomenheden in het glas die uiteindelijk kunnen leiden tot spontaan versplinteren. Na verloop van tijd kunnen vuurvaste stenen bijvoorbeeld van het materiaal in de glasmix beginnen te sijpelen. Ovens moeten daarom om de paar jaar worden stilgelegd voor onderhoud en opnieuw worden bekleed.
Vorming van Shell
Dit vindt plaats op een geautomatiseerde pers waarbij een precieze hoeveelheid gesmolten glas in de vormholte wordt gestoken en geperst (zie figuur 1). De afmetingen van elke specifieke schaal, dwz hoogte en diameter, zijn gedefinieerd door normen, maar de geometrie en het profiel van de schaal kunnen van leverancier tot leverancier verschillen.
Hardingsproces
Na het vormen doorloopt de schaal een speciaal proces waarbij het van de pers naar een hardingslijn wordt overgebracht en door een homogenisatieoven gaat om het glas op een constante hoge temperatuur te houden. Glasharding wordt bereikt door het hete glas snel af te koelen met behulp van perslucht op belangrijke locaties langs de schaal om een uniforme koeling te bereiken. Dit resulteert in het glas met een hete kerntemperatuur maar een relatief koel oppervlak. De glasstructuur na harding ziet het midden onder spanning staan terwijl het oppervlak onder druk staat en dit verhoogt zowel de mechanische en elektrische weerstand als de duurzaamheid van de glazen isolerende delen. Het bereiken van een uniforme hoge kwaliteit in deze kritieke stap vereist een sterk geautomatiseerd en zorgvuldig gecontroleerd materiaalverwerkingsproces.
Thermische cyclus
Na harding worden de schalen overgebracht door een voorgeschreven thermische cyclus, waar ze een thermische schok krijgen met als doel potentieel defecte schalen eruit te halen. De schelpen worden verwarmd tot ongeveer 300°C en vervolgens in koud water gedropt, waardoor de temperatuur van het glas effectief daalt tot 120°C. Onvoldoende geharde glazen schalen zullen instorten door de plotselinge thermische schok. Elke schaal wordt minimaal één keer thermisch getest en indien nodig kan het hele proces worden herhaald. De thermische schokcyclus is in wezen een belangrijke kwaliteitscontrole, aangezien elke schaal die springt een"Niet gaan"terwijl schelpen die overleven een 'Go' zijn. Die glazen schalen die instorten tijdens thermische cycli worden gerecycled, waarbij fragmenten worden verzameld en weer worden toegevoegd aan het productieproces in de vorm van glasscherven (zaadglas).
Werking van de oven is"24/7"en dus sneller dan het montageproces. Om deze reden worden voltooide schalen op voorraad gehouden totdat ze klaar zijn voor montage. Cap & Pin Assembly Glazen schalen worden in de kappen gecementeerd, terwijl de pin en zinkhulzen in de schaal worden gecementeerd met aluminiumoxidecement. Ook hier wordt automatisering gebruikt om een nauwkeurig afgemeten hoeveelheid cement te garanderen en een nauwkeurige lengtetolerantie te bereiken. Het gecementeerde geheel wordt vervolgens uitgehard door het gedurende een uur door een bad in water van ongeveer 70°C te laten lopen. Na uitharding wordt elke isolator van gehard glas onderworpen aan elektrische en mechanische routinetests en aan visuele eindcontroles.
Routine elektrische test: continue flashover gedurende 4 minuten,
Routinematige mechanische test: gehouden op 50% van de SML-classificatie voor>3 sec.
Vervolgens worden steekproeven uitgevoerd op elke geassembleerde partij isolatoren. Dit omvat verificatie van alle kritieke afmetingen, conformiteit van de mof/kogelmeter, verificatie van het sluitsysteem, verzinkingscontrole, M&E-test en pulspunctietest.
Validatie- en testrapporten
Afgewerkte isolatoren zijn onderworpen aan ontwerp- of kwalificatietesten volgens industrienormen, waaronder ANSI C29-2B, IEC 60383, CSA-411-1-16 en GOST 6490-93. Klanten kunnen naast deze normen ook aanvullende testcriteria aan hun specificaties toevoegen om de uiteindelijke isolatieprestaties verder te kwalificeren.
Testrapporten voor elk isolatorontwerp moeten specifiek zijn voor de fabriek waar de isolator wordt vervaardigd. Als een leverancier twee fabrieken heeft die hetzelfde type isolator produceren, moeten er afzonderlijke ontwerp-/kwalificatierapporten zijn voor elke isolator die specifiek is voor de fabriek waar deze is gemaakt. Voor producten die op een andere locatie zijn geassembleerd, moeten testrapporten hiervoor verwijzingen bevatten naar de fabriek die de schaal heeft gemaakt. Als de schalen van gehard glas uit twee fabrieken komen, moet dat afzonderlijke testrapporten voorschrijven (dwz specifiek voor de fabriek die de schaal heeft vervaardigd).
Conclusies
Bij het overwegen van de kwaliteit van een isolator van gehard glas, moeten evaluatie en kwalificatie grondig zijn en elk aspect van de productie omvatten. Er moet extra aandacht worden besteed aan waar de schaal van gehard glas wordt vervaardigd en ook aan hoe dat proces wordt onderhouden om te voorkomen dat defecte schalen ooit worden gebruikt bij de assemblage van afgewerkte isolatoren. Dit komt omdat, hoewel de montage van de dop en de pin belangrijk is, de kwaliteit van de geharde glazen schaal een grotere invloed zal hebben op de isolatieprestaties op de lange termijn. Testrapporten moeten specifiek zijn voor de fabriek waar de isolator is geproduceerd, maar moeten ook verwijzen naar waar de schaal is vervaardigd. Hiervoor zijn specifieke fabrieksmarkeringen vereist. De behuizing van gehard glas moet minimaal markeringen hebben die in de behuizing zijn gegoten, inclusief M&E-classificatie, lotcodereferentie, en fabrieksidentificatie (ID). Deze markeringen moeten leesbaar en permanent zijn. De ID van de fabriek waar de isolator is gemonteerd, moet op de dop van de isolator worden vermeld – ook leesbaar en permanent. Zelfs als het in dezelfde fabriek is gemaakt, helpt het hebben van dergelijke markeringen op zowel de schaal als de dop om te identificeren wanneer de schaal is gemaakt en wanneer deze is gemonteerd. Het toevoegen van fabrieks-ID-markeringen aan de schaal is eenvoudig, heeft weinig invloed op de productkosten en biedt toch een hoger niveau van kwaliteitsborging voor de isolatoren. De verschillende industriestandaarden (bijv. ANSI, IEC, CSA) vragen niet specifiek om een fabrieks-ID op een shell, maar zouden dat misschien wel moeten doen. Zelfs als het in dezelfde fabriek is gemaakt, helpt het hebben van dergelijke markeringen op zowel de schaal als de dop om te identificeren wanneer de schaal is gemaakt en wanneer deze is gemonteerd. Het toevoegen van fabrieks-ID-markeringen aan de schaal is eenvoudig, heeft weinig invloed op de productkosten en biedt toch een hoger niveau van kwaliteitsborging voor de isolatoren. De verschillende industriestandaarden (bijv. ANSI, IEC, CSA) vragen niet specifiek om een fabrieks-ID op een shell, maar zouden dat misschien wel moeten doen. Zelfs als het in dezelfde fabriek is gemaakt, helpt het hebben van dergelijke markeringen op zowel de schaal als de dop om te identificeren wanneer de schaal is gemaakt en wanneer deze is gemonteerd. Het toevoegen van fabrieks-ID-markeringen aan de schaal is eenvoudig, heeft weinig invloed op de productkosten en biedt toch een hoger niveau van kwaliteitsborging voor de isolatoren. De verschillende industriestandaarden (bijv. ANSI, IEC, CSA) vragen niet specifiek om een fabrieks-ID op een shell, maar zouden dat misschien wel moeten doen.